Ceramic Sanding Belts Vs Aluminum Oxide
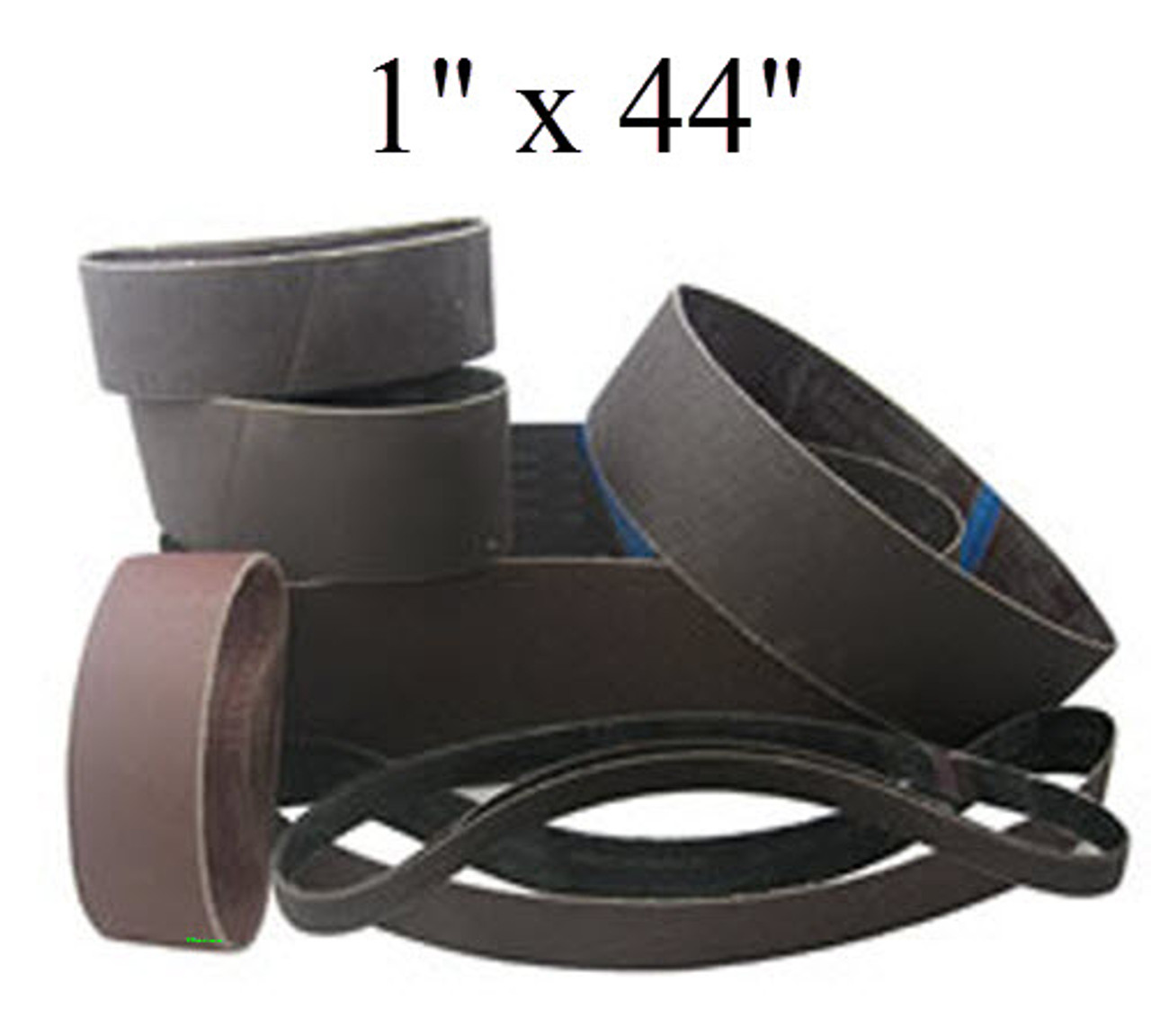
In the end both types of belts are excellent belts.
Ceramic sanding belts vs aluminum oxide. To see how different brands of sandpaper stack up see torture test. When sanding harder metals such as titanium or stainless steel aluminum oxide does not have as long of a life as say ceramic or zirconia. Both grains are considered hi performance. This habit means that ceramic grains break down in a controlled manner extending the.
Open coat resists loading due to spreading the grains apart on the backing material. Flap discs sanding discs quick change discs wide range of belts ceramic grit abrasives. Available in open and closed coat. Ceramic abrasives have a micro crystalline habit and are more uniform in their structure than either aluminium oxide or zirconia abrasives.
As high performance belts both zirconia and ceramic sanding belts will last longer and remove metal faster than aluminum oxide or silicon carbide sanding belts. The combination of a very good shelf life and lower cost is what makes aluminum oxide stand out over other forms of sandpaper including silicon carbide. Most versatile abrasive for use on all wood sanding applications from stock removal to finish sanding. Although it is stronger than aluminum oxide zirconia may have difficulties grinding mill scale.
Zirconia will have a much longer life than aluminum oxide be more fiable and provide a cooler sanding grinding experience. Recognized by its brownish red color. Used primarily on metal applications. On the other hand closed coat sandpaper produces a more uniform scratch pattern making it a good choice for sanding finishes.
Aluminum oxide is the most common abrasive used on sandpaper. Zirconia sanding discs and zirconia sanding belts are the most popular types of abrasives found in the marketplace. Both belts have the ability to resharpen as they wear and both are primarily used on metal applications. Both will remove metal faster and last longer than all aluminum oxide or silicon carbide products.